Drehgestell der neuesten Generation
Ein weiterer Meilenstein in der Entwicklung eines neuartigen Drehgestellrahmens für den Schienenverkehr ist erreicht – der Startschuss für den Beginn der Fertigung des Längsträger-Demonstrators „hybridBOGIE“ (Englisch für Hybrid-Drehgestell) ist gefallen. Die HÖRMANN Vehicle Engineering GmbH mit Sitz in Chemnitz arbeitete gemeinsam mit ihrem Projektpartner, dem Institut für Konstruktion und Verbundbauweisen gemeinnützige GmbH, Ende 2020 intensiv am Fertigungswerkzeug sowie an der Erarbeitung und Verfeinerung des Fertigungsprozesses, um ein seriennahes Referenzbauteil des Längsträgers zu entwickeln. „Neben der eigentlichen Prozessvalidierung, dient die Längsträgerkomponente im weiteren Projektverlauf auch für weitere Untersuchungen bis hin zur Testung und Bewertung von mechanischen Parametern sowie den Federungseigenschaften“, erklärt Matthias Büttner, Projektleiter bei HÖRMANN Vehicle Engineering.
Anfang 2019 startete das Förderprojekt hybridBOGIE der Sächsischen Aufbaubank. Projektpartner sind das Institut für Konstruktion und Verbundbauweisen gemeinnützige GmbH (KVB), das Fraunhofer-Institut für Werkzeugmaschinen und Umformtechnik (IWU), die IMA Materialforschung und Anwendungstechnik GmbH (IMA) und die HÖRMANN Vehicle Engineering GmbH (HVE). Ziele des Projektes sind eine Gewichtseinsparung von 75 Prozent gegenüber einem konventionellen Drehgestellrahmen, die Integration der Primärfeder, eines Steinschlagschutzes und Sensornetzwerkes in den Rahmen, die Erarbeitung eines Degradationsmodelles zur Bestimmung der Restlebensdauer des Faserverbundes und die Entwicklung eines speziell auf den Hybrid-Verbund angepassten Prüfverfahrens.
Fertigung von Prototypenteilen für Nachweis der Vorteile
Im ersten Jahr der dreijährigen Projektlaufzeit entwickelte HÖRMANN Vehicle Engineering den Drehgestellrahmen aus Hybrid-Material und integrierte neben der Primärfeder auch die Funktion des Brandschutzes in den Drehgestellrahmen. Das KVB erarbeite parallel Lösungen für den Steinschlagschutz und die Integration des Sensornetzwerkes zur Zustandsüberwachung des Rahmens. Das IWU entwarf Versagenskriterien und integrierte diese in die Software ANSYS. Für die Qualitätssicherung nach der Fertigung und vor dem Ermüdungstest wurden Korrekturfaktoren der Berechnung auf relevante Dimensionen durch die IMA untersucht.
2020 erarbeiteten HÖRMANN Vehicle Engineering und das KVB einen geeigneten Fertigungsprozess für den Drehgestell-Längsträger und das dafür notwendige Werkzeug. Wie beim Prototypenbau für hochbeanspruchte Komponenten üblich, wurde der Autoklavprozess für die Aushärtung des Faser-Kunststoff-Verbundes gewählt. Die IMA führte 2020 Vortests an relevanten Faserverbunden mittels Ultraschall durch und optimierte Frequenzen und Schallschwächungsfaktoren. Ende 2020 stellte der Unterauftragnehmer Modellbau Roth GmbH & Co. KG das Werkzeug für den Drehgestell-Längsträger her. „All diese Schritte führen zu einem Drehgestell mit besseren Parametern in der Funktionalität, im Gewicht, in der Laufleistung und der Geräuschemission“, so Frank Salzwedel, Geschäftsführer von HÖRMANN Vehicle Engineering.
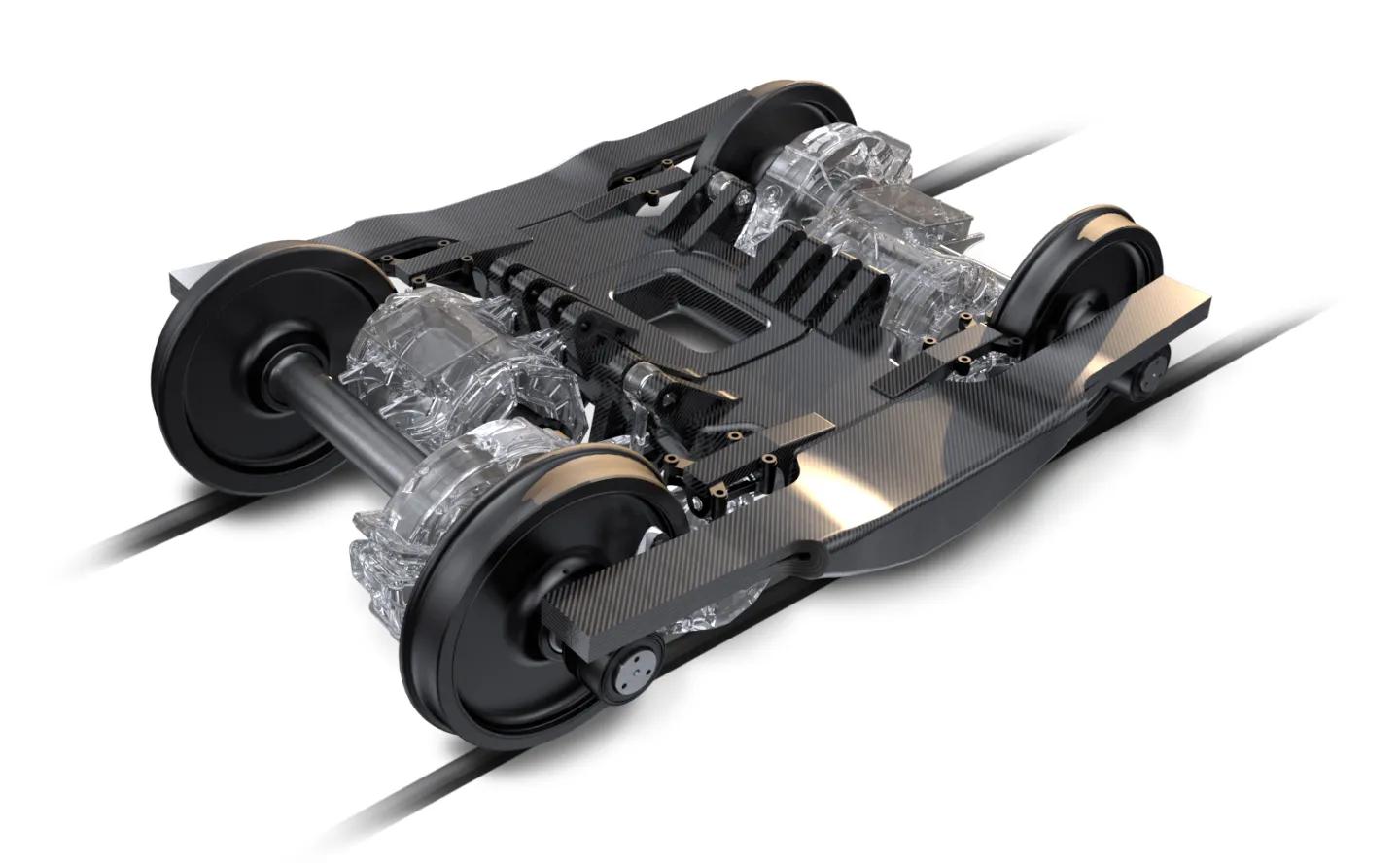