Latest generation bogie
Another milestone has been reached in the development of a new type of bogie frame for rail transport - the go-ahead has been given for the start of production of the "hybridBOGIE" (hybrid bogie) side member demonstrator. HÖRMANN Vehicle Engineering GmbH, based in Chemnitz, worked intensively with its project partner, the Institut für Konstruktion und Verbundbauweisen gemeinnützige GmbH, on the production tool and on developing and refining the production process at the end of 2020 in order to develop a near-series reference component for the side member. "In addition to the actual process validation, the side member component will also be used for further investigations in the further course of the project, including the testing and evaluation of mechanical parameters and suspension properties," explains Matthias Büttner, Project Manager at HÖRMANN Vehicle Engineering.
The hybridBOGIE funding project of the Sächsische Aufbaubank started at the beginning of 2019. The project partners are the Institut für Konstruktion und Verbundbauweisen gemeinnützige GmbH (KVB), the Fraunhofer Institute for Machine Tools and Forming Technology (IWU), IMA Materialforschung und Anwendungstechnik GmbH (IMA) and HÖRMANN Vehicle Engineering GmbH (HVE). The aims of the project are to achieve a weight saving of 75 percent compared to a conventional bogie frame, to integrate the primary spring, a stone guard and sensor network into the frame, to develop a degradation model to determine the remaining service life of the fiber composite and to develop a test method specially adapted to the hybrid composite.
Production of prototype parts to demonstrate the advantages
In the first year of the three-year project, HÖRMANN Vehicle Engineering developed the bogie frame made of hybrid material and integrated the fire protection function into the bogie frame in addition to the primary spring. In parallel, the KVB developed solutions for stone impact protection and the integration of the sensor network for monitoring the condition of the frame. The IWU developed failure criteria and integrated these into the ANSYS software. For quality assurance after production and before the fatigue test, correction factors of the calculation were examined for relevant dimensions by the IMA.
In 2020, HÖRMANN Vehicle Engineering and the KVB developed a suitable manufacturing process for the bogie longitudinal member and the tool required for this. As is usual in prototype construction for highly stressed components, the autoclave process was chosen for curing the fiber-plastic composite. In 2020, IMA carried out preliminary tests on relevant fibre composites using ultrasound and optimized frequencies and sound attenuation factors. At the end of 2020, the subcontractor Modellbau Roth GmbH & Co. KG produced the tool for the bogie longitudinal member. "All these steps lead to a bogie with better parameters in terms of functionality, weight, mileage and noise emissions", says Frank Salzwedel, Managing Director of HÖRMANN Vehicle Engineering.
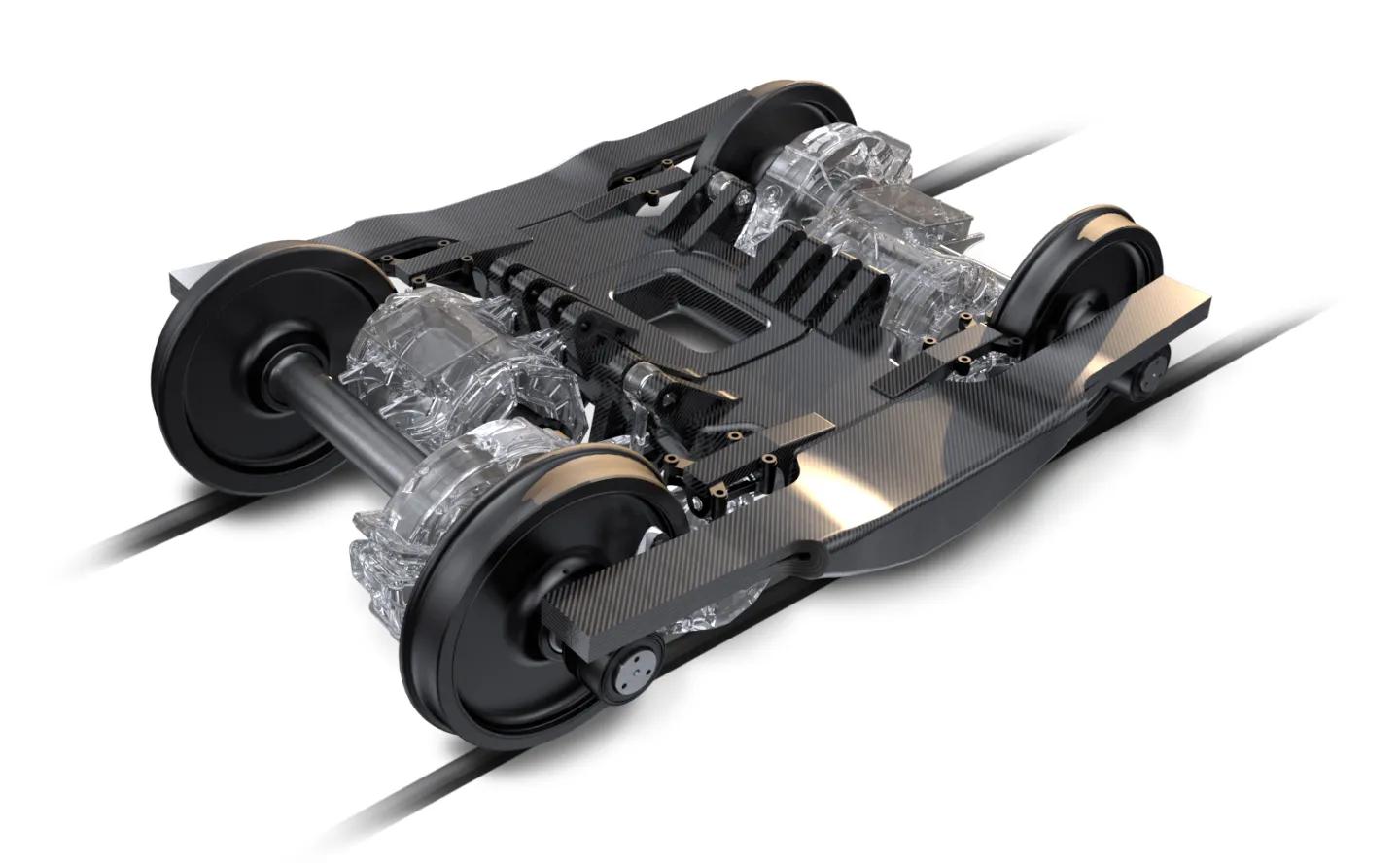