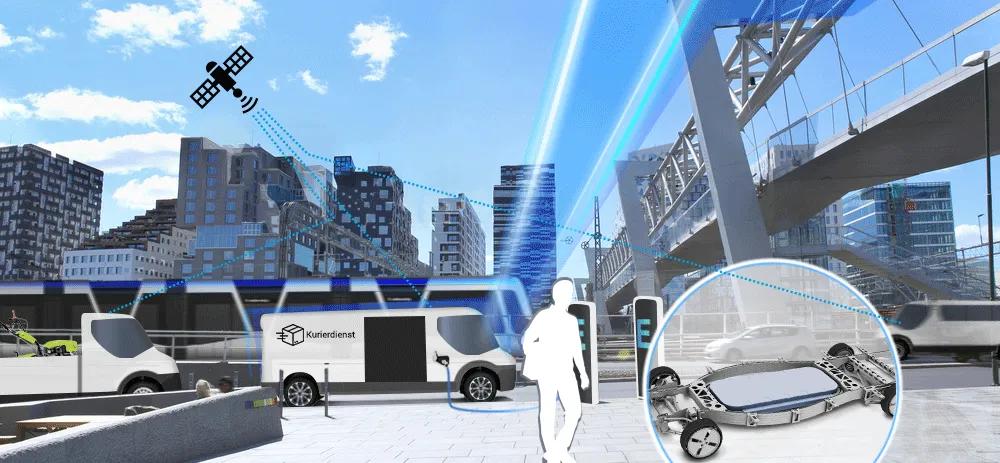
Lightweight construction
3D-FiberTrain
Development of a tool-free manufacturing process for the production of large-format and highly resilient rail vehicle components
Project period: Sep 2023- Jun 2026 | Project partners: Fraunhofer IWU, Lakowa Kunststoffbe- und verarbeitungs GmbH, Siemens Mobility GmbH (associated)
The research consortium around HÖRMANN Vehicle Engineering is researching and developing an innovative thermoplastic technology that combines large-format 3D printing with the 3D tape laying process. This method enables the tool-free production of complex and resilient large components for rail vehicles, such as front masks and roof structures. Especially for small to medium series sizes, additive thermoplastic processes offer considerable optimization potential in terms of costs, time and materials as well as a reduction in the CO2 footprint. The elimination of moulding tools, a high degree of automation and the use of reusable materials lead to lower manufacturing costs and improved resource efficiency compared to conventional thermoset fiber composite processes.
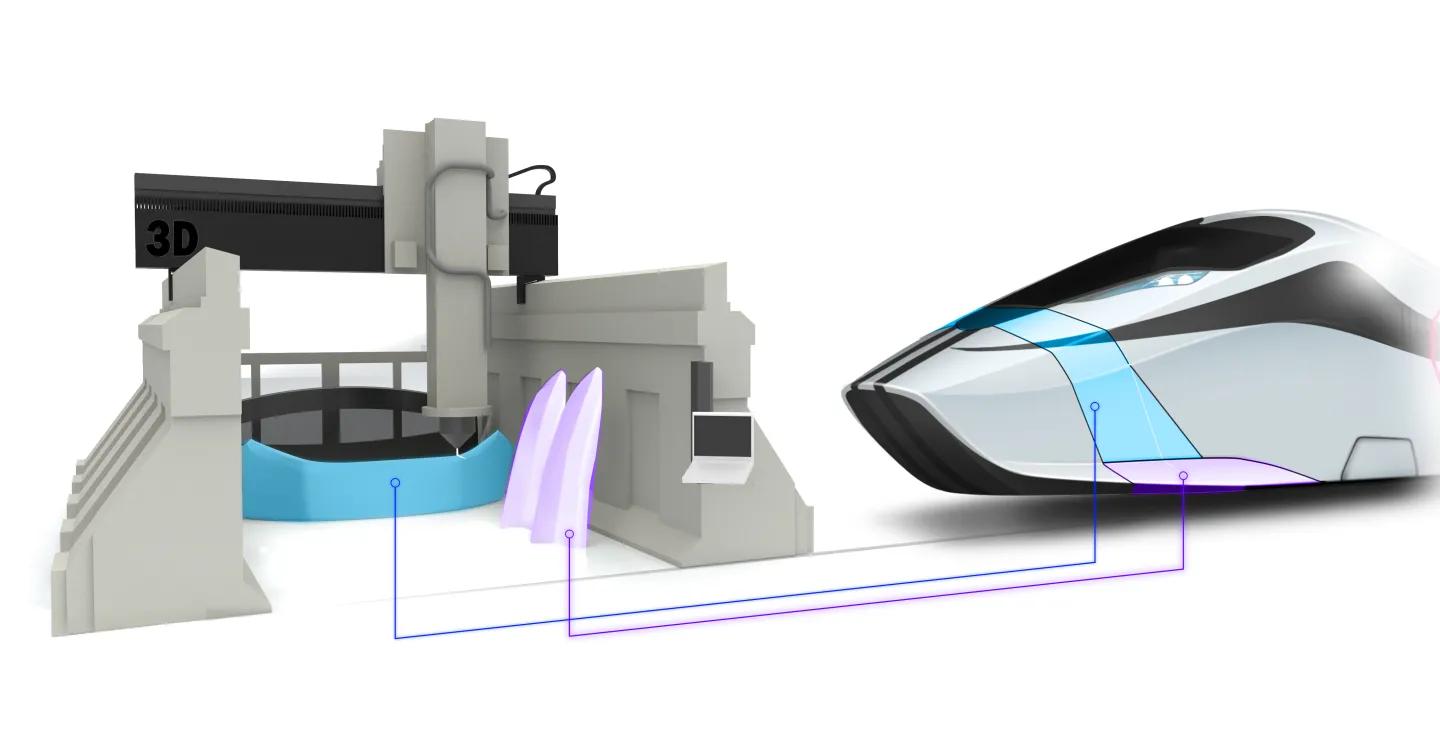
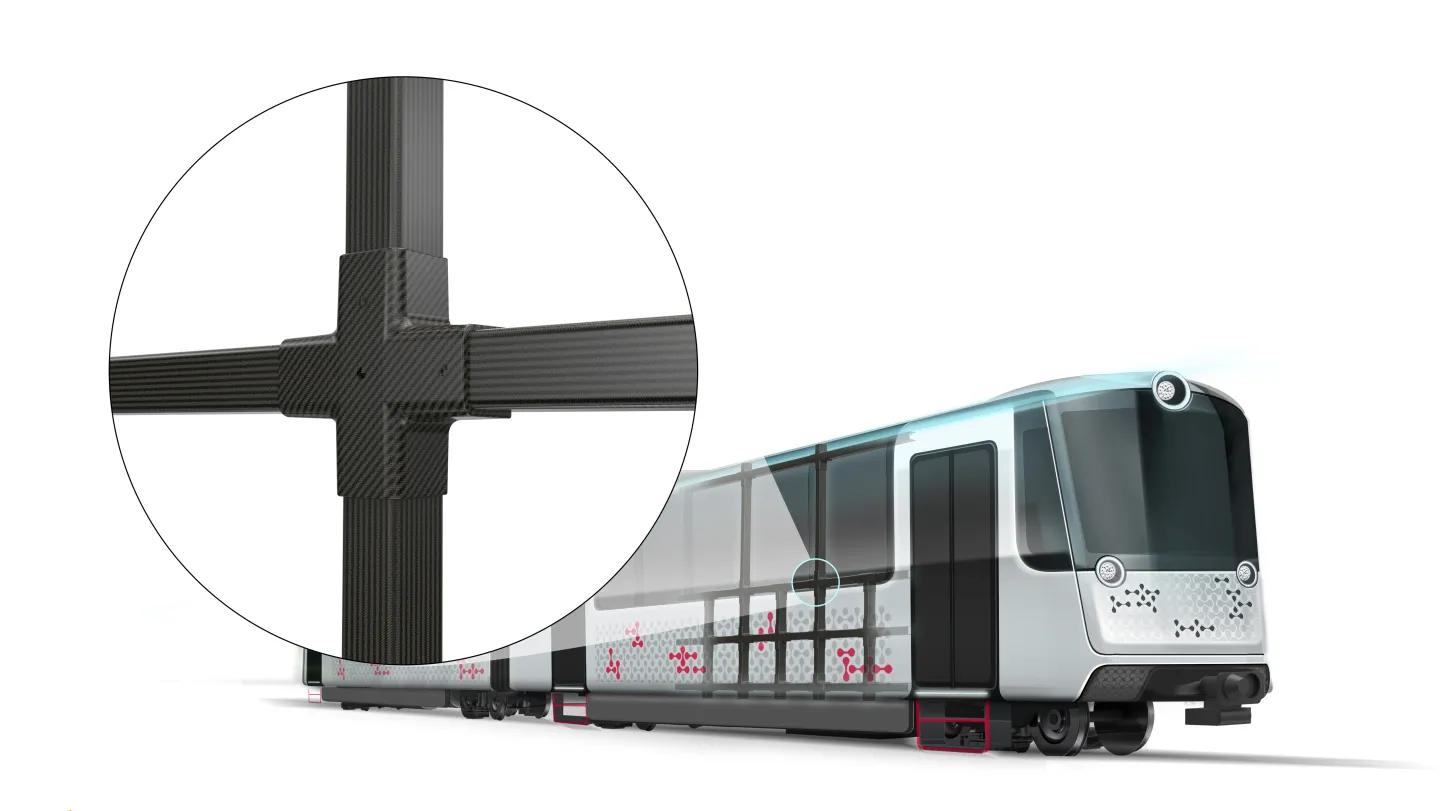
PulPro - SMC
Use of pultrusion profiles in combination with load-path-compatible SMC made of recycled carbon fibers in body-in-white structures of rail vehicles
Project period: Oct 2023- Jun 2026 | Project partners: Conbility GmbH, Fraunhofer IWU, LSE-Lightweight Structures Engineering GmbH, Modellbau Roth GmbH & Co. KG, Polynt Composites Germany GmbH
In order to bring together and further develop different perspectives and applications of the cross-sectional technology of lightweight construction, the PulPro-SMC R&D project under the leadership of HVE GmbH specifically combines expertise from several lightweight construction disciplines. The focus is on the resource-saving production of structural components made of fiber-reinforced plastics for the mass markets on road and rail. The aim is to produce a material-locking frame structure from pultruded fiber composite profiles as an alternative to the conventional method of combining welding and steel profiles. In particular, the combination of the generally contradictory areas of lightweight construction, crash safety and cost-effectiveness represents a major challenge in the PulPro-SMC project. The overall objective is to realize an efficient and economical manufacturing technology for fibre-reinforced lightweight vehicle structures using a modified pultrusion process in combination with a load-path-reinforced recycled SMC shaping process. The proof of technology is to be provided using a real rail vehicle component.
LeiPo-3D-FKM
Development of new lightweight construction potential through standardized design of components for metallic 3D printing using FKM guidelines
Project period: Jan 2025- Dec 2027 | Project partners: IMK Engineering GmbH, BMF GmbH - Bernstein Mechanische Fertigung, SWM Struktur- und Werkstoffmechanikforschung gGmbH, TU Chemnitz - Professur Strukturleicht-bau und Kunststoffverarbeitung
HÖRMANN Vehicle Engineering is committed to achieving global climate targets for energy efficiency and resource conservation. In the field of lightweight metal construction, innovative production methods such as additive manufacturing open up considerable potential for mass reduction. In order to establish this technology more broadly, a standardized design of additively manufactured components is necessary. The FKM guideline plays a central role here, but it does not currently integrate metallic 3D printing and its post-processing methods. This significantly limits the innovative power of companies that have to design according to FKM.
The LeiPo-3D-FKM consortium aims to solve this problem and develop an additively manufactured steel alloy for FKM qualification. Important influencing factors such as powder condition and AM system technology as well as post-processing conditions, in particular surface smoothing and compaction, are taken into account. The application partners transfer this knowledge to representative technology carriers in transportation and mechanical engineering and validate it through testing.
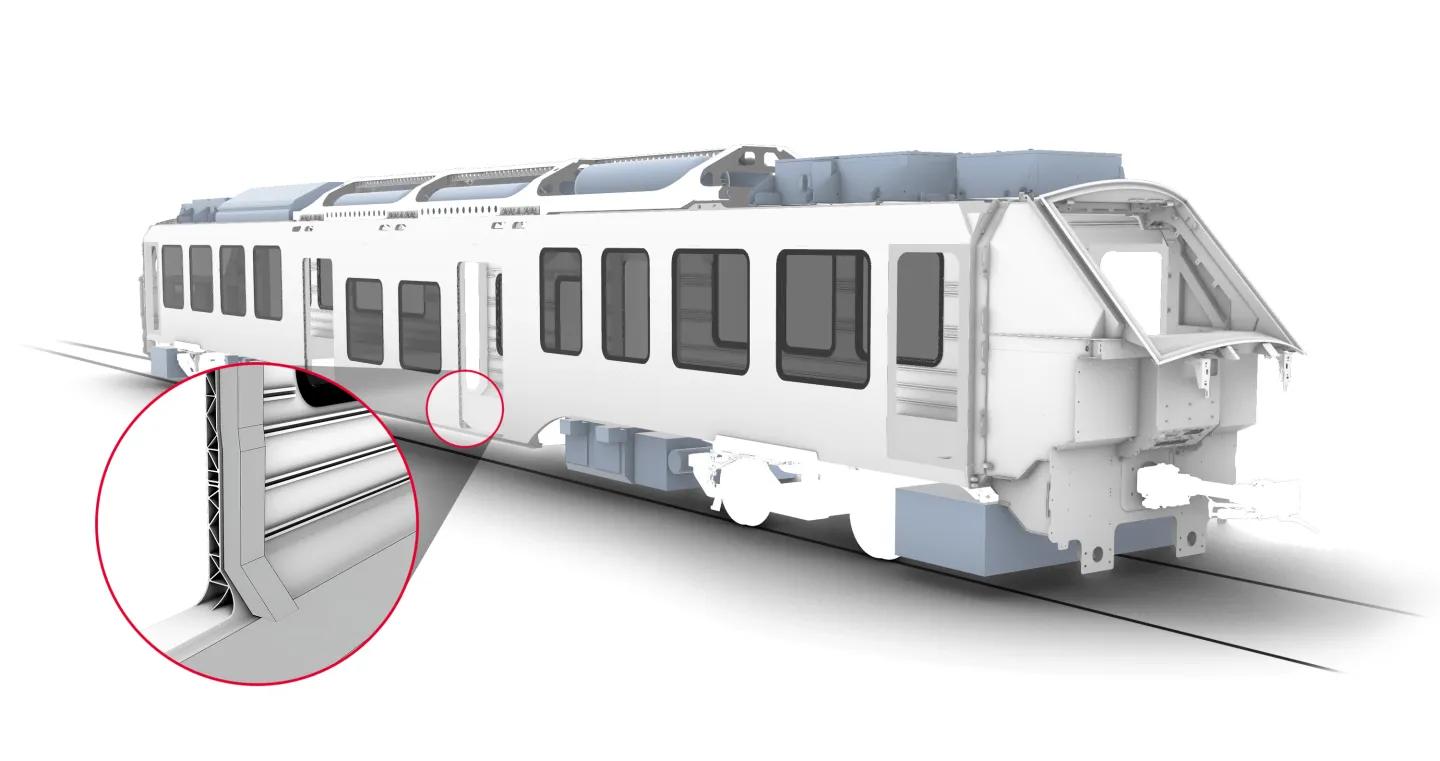
AnoWaAs
Development of a novel and modular car body for rail vehicles
Project duration: May 2021 - April 2024 | Project partners: ALSTOM, DLR - Institute of Vehicle Concepts, elemag GmbH, GSI mbH Branch SLV Berlin-Brandenburg, Rausch Metalltechnik GmbH, University of Stuttgart - Institute for Machine Elements, 3A Composites GmbH
The project involves the systematic development of a new type of modular car body for rail vehicles. In terms of structure and architecture, this will be adapted as optimally as possible to alternative drive systems (battery and fuel cell). The aim is to optimally integrate the heavy components, taking into account the mechanical vehicle body architecture and significant lightweight construction. Cost efficiency, production, maintenance and recycling are given particularly high priority. Various methods are used to map the entire development chain: from fundamental, process-based packaging studies to construction method developments, innovative design and layout processes, optimized manufacturing and assembly processes and the prototypical implementation of exemplary components, with the focus always on lightweight construction. The similarities between commercial vehicle bodies and the bodies of rail vehicles are exploited and recognized synergies between the two areas are consistently pursued. The consortium therefore includes partners with expertise in both sectors and beyond. The results will contribute to strengthening the German economy in lightweight construction and to CO2 savings.
INTEGRAL (completed research project)
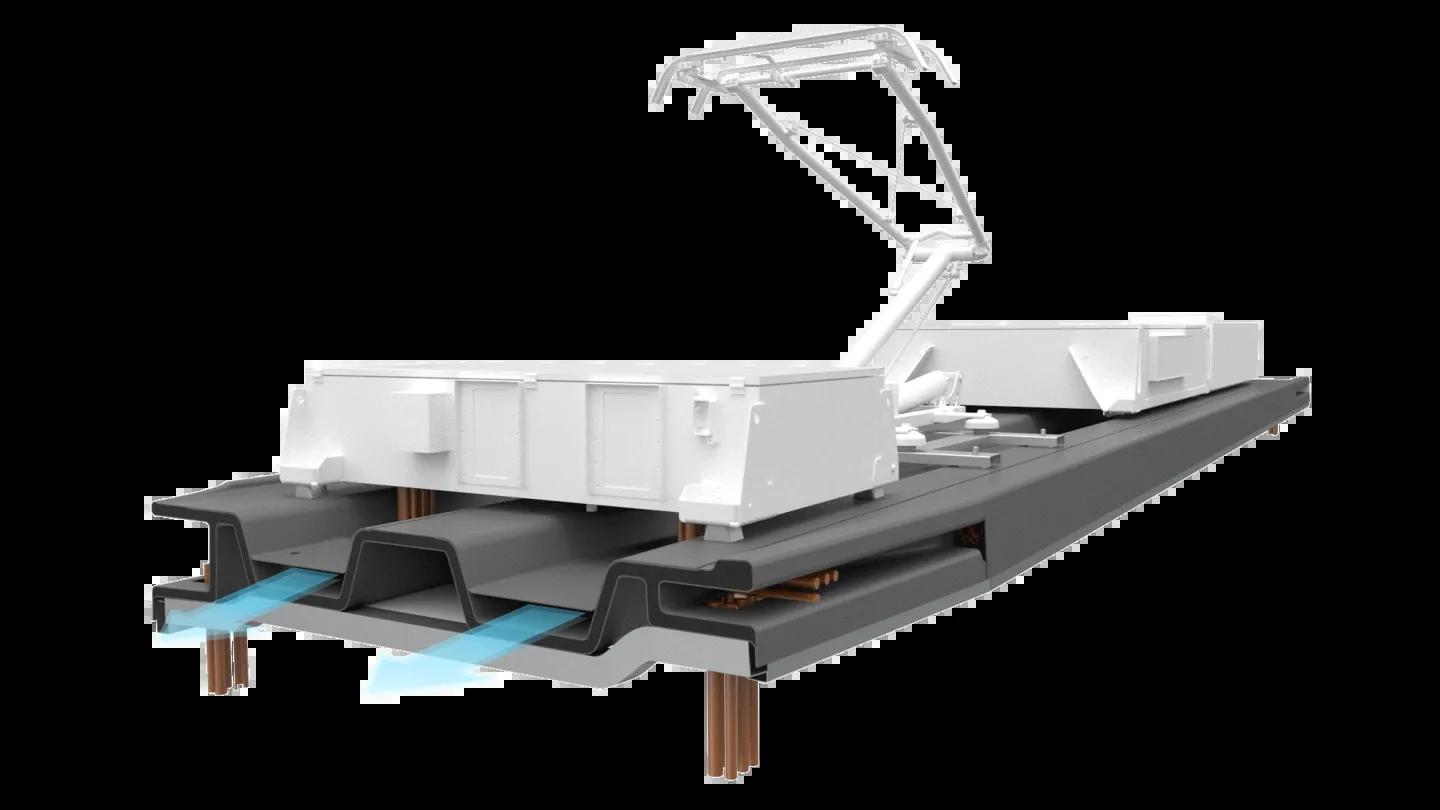
FunPul (completed research project)
RESOLVE (completed research project)
Im research project RESOLVE should now the qualification of the technology approaches in the field of experimental development is to be advanced - and precisely fitting, bionically supported construction methods and Construction methods can be developed. The associated significant increase in cost-effectiveness, resource efficiency and productivity can lead to a significant expansion and diversification of the fields of application of continuous fiber-reinforced thermoplastic fiber composite materials, which will bring intelligent and climate-friendly lightweight construction solutions into broad industrial application. Due to the highly interdisciplinary nature of the development content, cross-industry knowledge and technology transfer will be promoted in line with the funding policy objectives, making a valuable contribution to securing Germany as an industrial location. In addition, as outlined in Chapter V, the project can make a significant contribution to achieving the climate targets.
This project was funded by: Federal Ministry for Economic Affairs and Climate Protection and Projektmittelräger Jülich (PtJ)
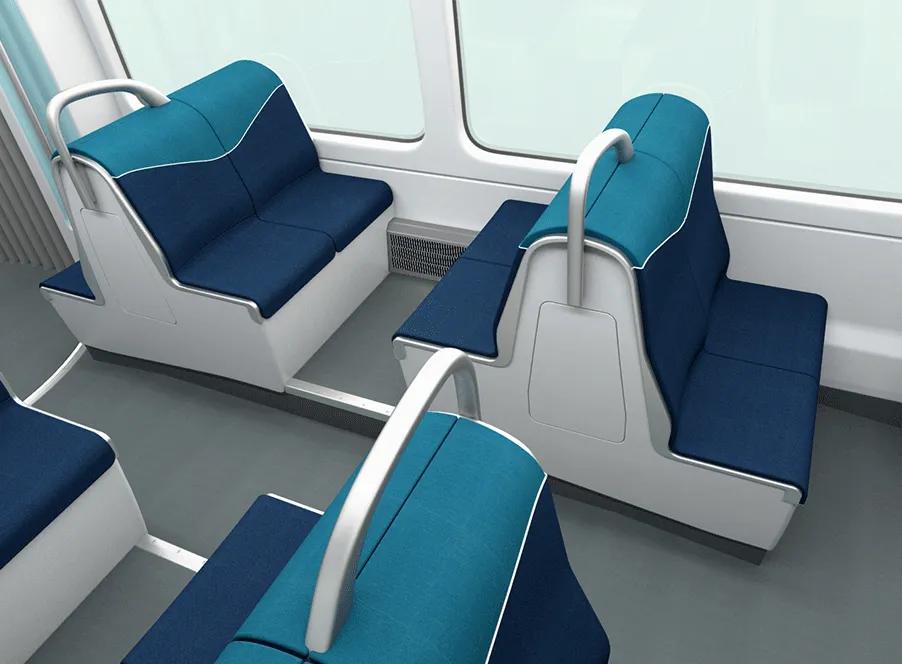
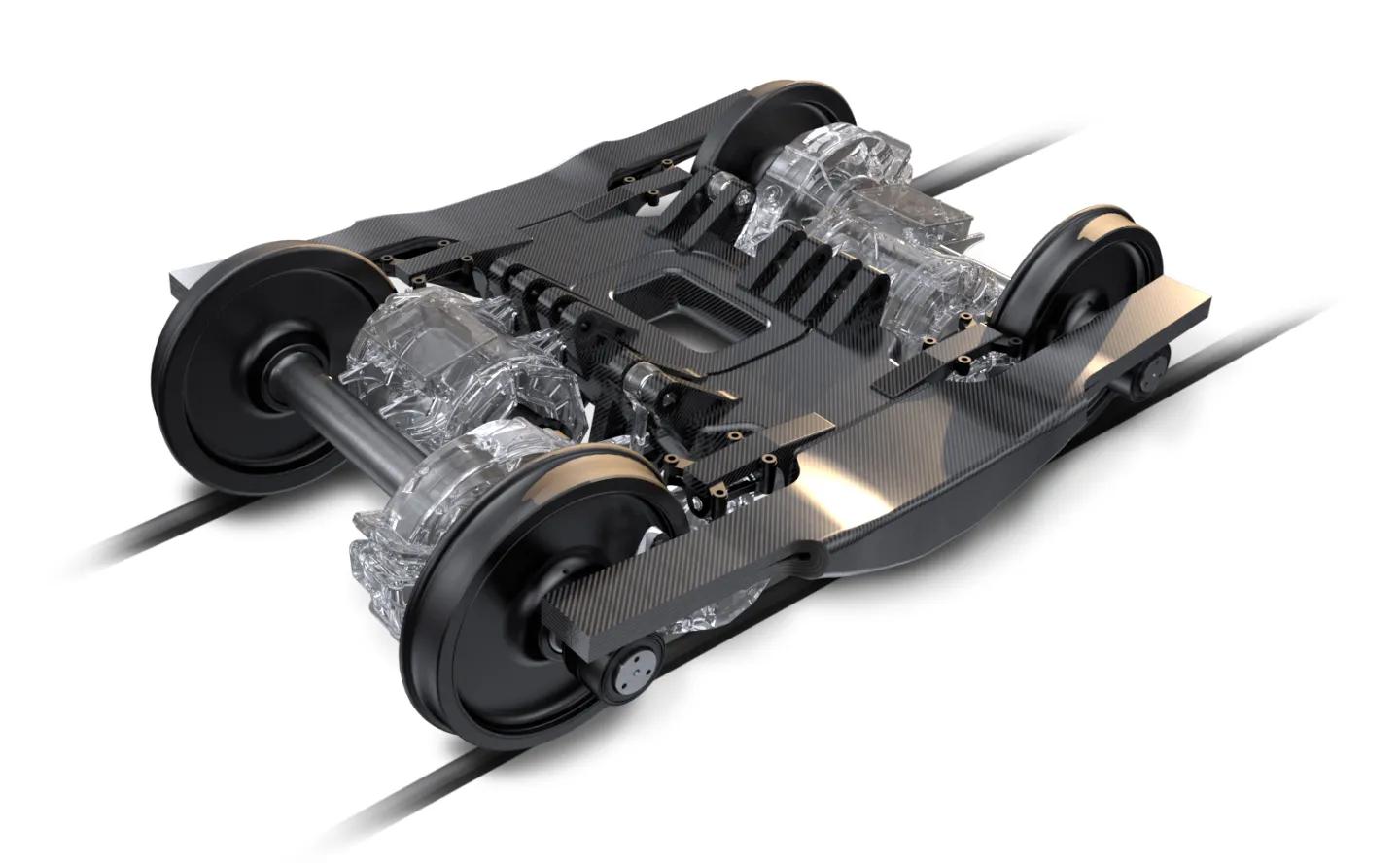
hybridBogie (completed research project)
HÖRMANN Vehicle Engineering developed a bogie (DG) of the latest generation as part of the hybridBOGIE joint project. The result was a bogie with better parameters in terms of functionality, weight, mileage and noise emissions. This was achieved by researching a hybrid mixed construction with vibration-damping materials and the active integration of suspension elements into the functional structure of the bogie frame (DGR).
The aim of the project was to develop a manufacturing process for the production of a hybrid fiber bogie frame, including demonstrator and prototype construction. The design and integration of a sensor network in the bogie frame for permanent component monitoring is also part of the sub-project. A concept for protecting the impact-sensitive frame structure from stone chipping was also researched.
This project was funded by: EFRE and SAB
thermoPre plus (completed research project)
In the joint project with regional industrial partners and research institutions, lightweight fiber-reinforced plastic composites (FRP) with their special mechanical properties (high-performance polymers) were to be processed into semi-finished products, so-called prepregs, and used for high-performance structural components in automotive and rail vehicle construction. As composite coordinator, HÖRMANN Vehicle Engineering designed an innovative one-piece streetcar seat based on innovative load-dedicated fiber composite structures (effiload semi-finished products). This is 25 percent lighter than comparable seat components and minimizes the assembly effort considerably. Such thermoplastic fiber composite components have great potential for series applications due to their short cycle times during component production.
This project was funded by: Federal Ministry of Education and Research and Projektmittelräger Jülich (PtJ)
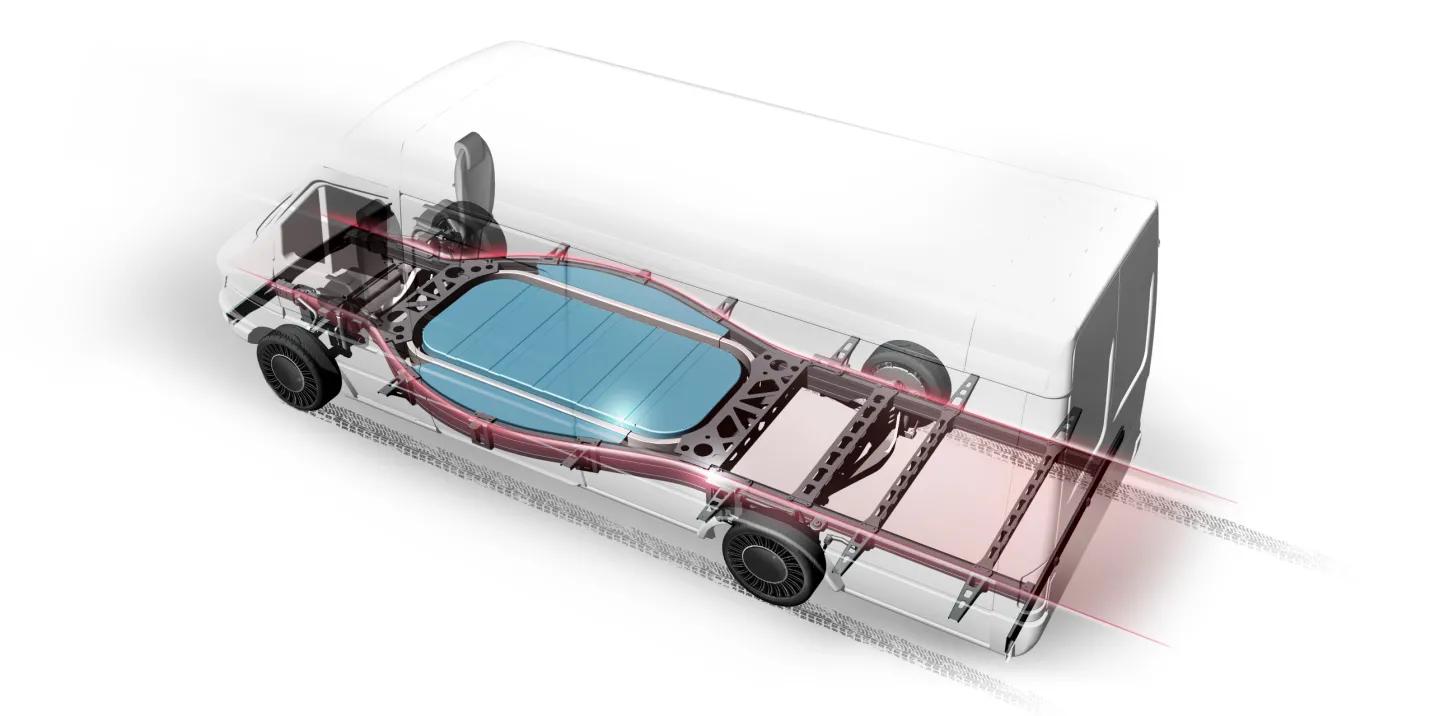
Innovative lightweight chassis (completed research project)
HÖRMANN Vehicle Engineering supported HÖRMANN Automotive GmbH in the development of a new integral chassis concept for light commercial vehicles. In terms of production technology, the concept is based on the results of the successfully completed Collaborative Research Center 666 "Integral Sheet Metal Structures of Higher Branching Order - Development, Production, Evaluation" at TU Darmstadt. It applies the technologies developed there to a vehicle construction application for future urban delivery traffic. It uses the branched sheet metal structures to implement new protection mechanisms for energy storage systems in vehicles with alternative drive systems.