Chassis modeled on nature
The topology of the new integral chassis concept for light commercial vehicles from HÖRMANN Automotive GmbH is oval like the shape of a nut or tortoise, making it both safe and light in terms of internal energy storage. In terms of production technology, the concept is based on the results of the successfully completed Collaborative Research Center 666 "Integral Sheet Metal Structures of Higher Branching Order - Development, Production, Evaluation" at TU Darmstadt. It applies the technologies developed there to a vehicle construction application for future urban delivery traffic. It uses the branched sheet metal structures to implement new protection mechanisms for energy storage systems in vehicles with alternative drive systems.
"For production research, the implementation of results from scientific research in industrial preliminary and series development projects is eminently important in order to ensure the coherence of university research and current challenges of industrial production," emphasizes Professor Peter Groche, Head of the Institute of Production Engineering and Forming Machines (PtU) at TU Darmstadt and former spokesperson of the SFB 666. "We have based our chassis development on nature," says Dr. Wolfram Schmitt, Head of Central Research and Development at HÖRMANN Automotive GmbH: "It is known from existing studies that oval structures can have a more favorable deformation behavior when used in the vehicle chassis compared to rectangular structures in the event of a crash. Nature also uses oval shapes to give its inner life special protection. We use this mechanism to protect the energy storage units of alternative drive systems in the chassis. This enables us to reduce the complexity of current protection systems such as battery boxes. With the research results of the SFB 666, we were able to transform the original idea into an innovative and at the same time economically attractive production and material concept."
Cooperation with TU Darmstadt and DLR
The overall chassis development was the result of a network in which the German Aerospace Center (DLR) was also involved alongside the PtU at TU Darmstadt. This cooperation made it possible to confirm the original idea of the oval shape through topological optimization. The production engineering implementation was then carried out in close cooperation with the production researchers at TU Darmstadt. In line with the basic topological idea and using the methods and forming processes developed in the SFB 666, non-linear multi-chamber profiles made of steel were developed, which ensure the protective function of the internal energy storage unit through the possibility of a load-adaptive design. "In the side member of the integral chassis, the knowledge gained in the SFB 666 is used in an exemplary manner, because the forming mechanisms of gap profiling are not only used to form the integral branching, but also to bend the high-strength profiles. This combination makes the bending process easier and enables significantly improved shaping accuracy of the branched, non-linear structural components compared to previous technologies," says Peter Groche.
The resulting approach of efficient structural lightweight construction brings economic benefits and promises a promising path, especially against the background of the consistent equipping of light commercial vehicles with alternative drive systems. PtU Darmstadt and HÖRMANN Automotive GmbH intend to continue along this path following the presentation of the vehicle concept at the IAA Commercial Vehicles 2018. "The ultimate application of our research results in industrial processes is an important goal of our work. In this respect, I am delighted that the integral chassis concept from HÖRMANN Automotive is an ideal example of how we can transfer our twelve years of research work into a production-ready application," says Peter Groche. Dr. Thomas Vetter, Managing Director of HÖRMANN Automotive GmbH, agrees: "In times of increasing urbanization on the one hand and the simultaneous threat of inner-city driving bans due to high carbon dioxide pollution on the other, we have to find solutions - also and especially for future inner-city delivery traffic. The collaboration with TU Darmstadt brings us a big step forward in this regard."
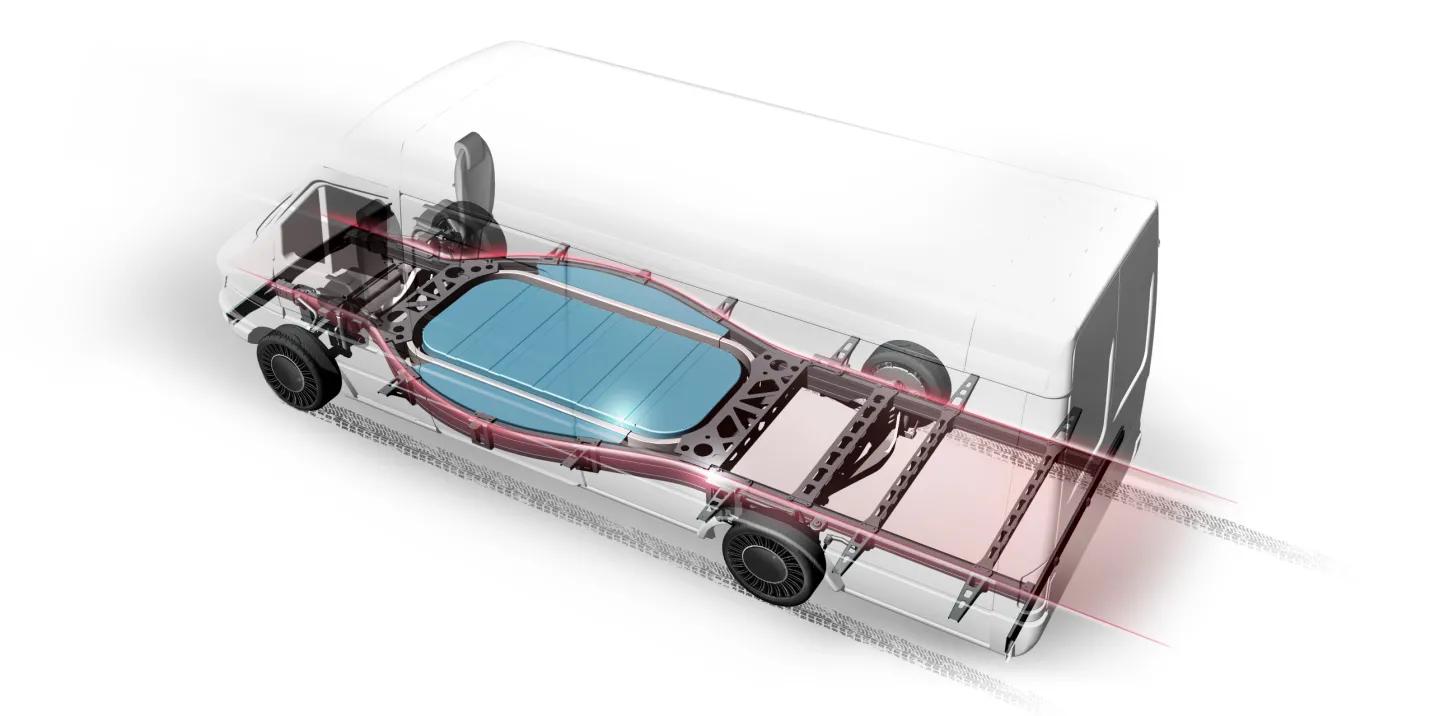