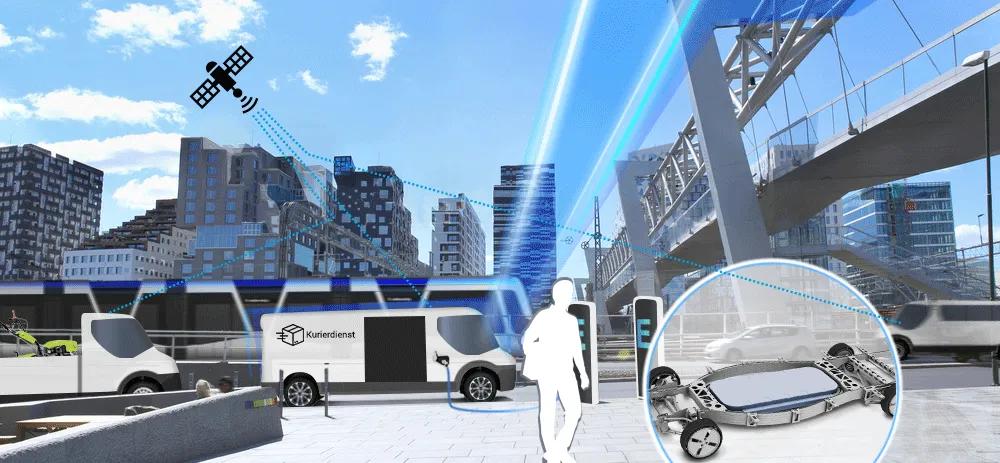
Lightweight
3-D FiberTrain
Entwicklung eines werkzeuglosen Fertigungsverfahrens zur Herstellung großformatiger und hochbelastbarer Schienenfahrzeugkomponenten
Projektzeitraum: Sep 2023- Jun 2026 | Projektpartner: Fraunhofer IWU, Lakowa Kunststoffbe- und verarbeitungs GmbH, Siemens Mobility GmbH (assoziiert)
Additive thermoplastische Kunststoffverarbeitungsverfahren bieten vollkommen neue Potentiale für eine deutliche Kosten-, Zeit- und Materialeinsparung sowie für eine Verringerung des CO2- Fußabdruckes insbesondere bei kleinen bis mittleren Seriengrößen. Das Forschungsvorhaben zielt auf die Erforschung und Entwicklung einer neuartigen thermoplastischen Technologie, die den Großformat-3D-Druck mit dem 3D-Tapelegeprozess kombiniert und dadurch die werkzeugfreie Fertigung von geometrisch komplexen und hochbelastbaren Großkomponenten für Schienenfahrzeuganwendungen – wie etwa Frontmasken, Dachstrukturen etc. – erlaubt. Der Verzicht auf Formwerkzeuge, der hohe Automatisierungsgrad sowie der Einsatz wiederverwendbarer thermoplastbasierter Ausgangsmaterialien führt unmittelbar zu reduzierten Herstellungskosten und einer deutlich verbesserten Ressourceneinsparung im Gegensatz zur konventionellen Fertigung solcher Schienenfahrzeugkomponenten mit klassischen duroplastbasierten Faserverbundverfahren.
Gefördert durch:

PulPro – SMC
Einsatz von Pultrusion-Profilen in Kombination mit lastpfadgerechten SMC aus recycelten Kohlenstofffasern in Rohbaustrukturen von Schienenfahrzeugen
Projektzeitraum: Okt 2023- Jun 2026 | Projektpartner: Conbility GmbH, Fraunhofer IWU, LSE-Lightweight Structures Engineering GmbH, Modellbau Roth GmbH & Co. KG, Polynt Composites Germany GmbH
Um unterschiedliche Perspektiven und Anwendungen der Querschnittstechnologie Leichtbau zusammenzubringen und weiterzuentwickeln, verbindet das FuE-Vorhaben PulPro-SMC unter Federführung der HVE GmbH gezielt Kompetenzen aus mehreren Leichtbau-Disziplinen mit dem Fokus der ressourceneffizienten – und damit CO2-reduzierten – Herstellung von serienfähigen Strukturbauteilen aus faserverstärkten Kunststoffen für die Massenmärkte auf Straße und Schiene. Speziell die Verknüpfung der sich nach allgemeinem Verständnis eher widersprechenden Bereiche Leichtbau, Crashsicherheit und Wirtschaftlichkeit stellt eine große Herausforderung in dem Projekt PulPro-SMC dar. Angestrebtes Gesamtziel ist die Realisierung einer effizienten und wirtschaftlichen Herstellungstechnologie für faserverstärkte Leichtbau-Fahrzeugstrukturen in einem modifizierten Pultrusionsverfahren in Kombination mit einem lastpfadgerecht verstärkten Recycling-SMC-Formgebungsprozess. Der Technologienachweis soll anhand einer realen Schienenfahrzeugkomponente geführt werden.
Gefördert durch:

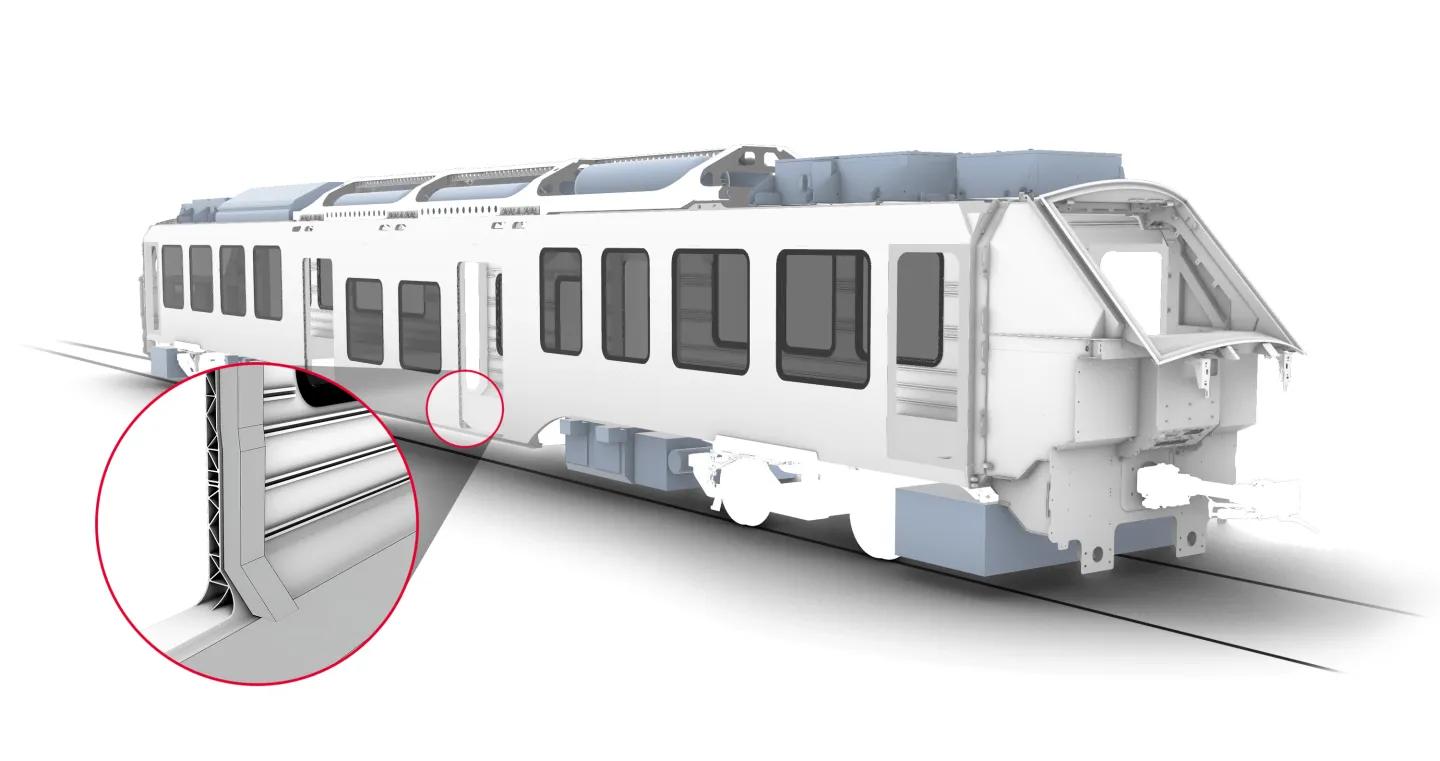
AnoWaAs
Development of a novel and modular car body for rail vehicles
Project period: Mai 2021 – April 2024 | Project partners: ALSTOM Transport Deutschland GmbH (Konsortialführerschaft), Deutsches Zentrum für Luft- und Raumfahrt e.V., Institut für Fahrzeugkonzepte, Elemag GmbH, GSI mbH Niederlassung SLV Berlin-Brandenburg, Rausch Metalltechnik GmbH, Universität Stuttgart, Institut für Maschinenelemente, 3A Composites GmbH (assoziierterPartner)
Within the scope of the project, a new type of modular car body for rail vehicles is being systematically developed which, in terms of its structure and architecture, is adapted as optimally as possible to alternative drive systems (battery and fuel cell). Due to the associated framework conditions, the optimized and integrated positioning of heavy components, the mechanical car body architecture and significantly lightweight construction, under the prerequisite of cost efficiency, are of particular importance, as are manufacturing, maintenance and recycling. Using a variety of methods, the complete development chain is mapped: from fundamental, process-based packaging studies to construction method developments, novel design and layout procedures, optimized manufacturing and assembly processes, and the prototypical implementation of exemplary components, with lightweight construction always in the foreground. The similarities between commercial vehicle bodies and the bodies of rail vehicles are being exploited and recognized synergies between the two areas are being consistently pursued in both directions. Therefore, the consortium includes partners with expertise in both sectors and beyond. For the reasons given, the results of the envisaged project will contribute to strengthening the German economy in lightweight construction and to CO2 savings.
INTEGRAL
Development and series production of competitive rail vehicle roofs in lightweight FKV construction
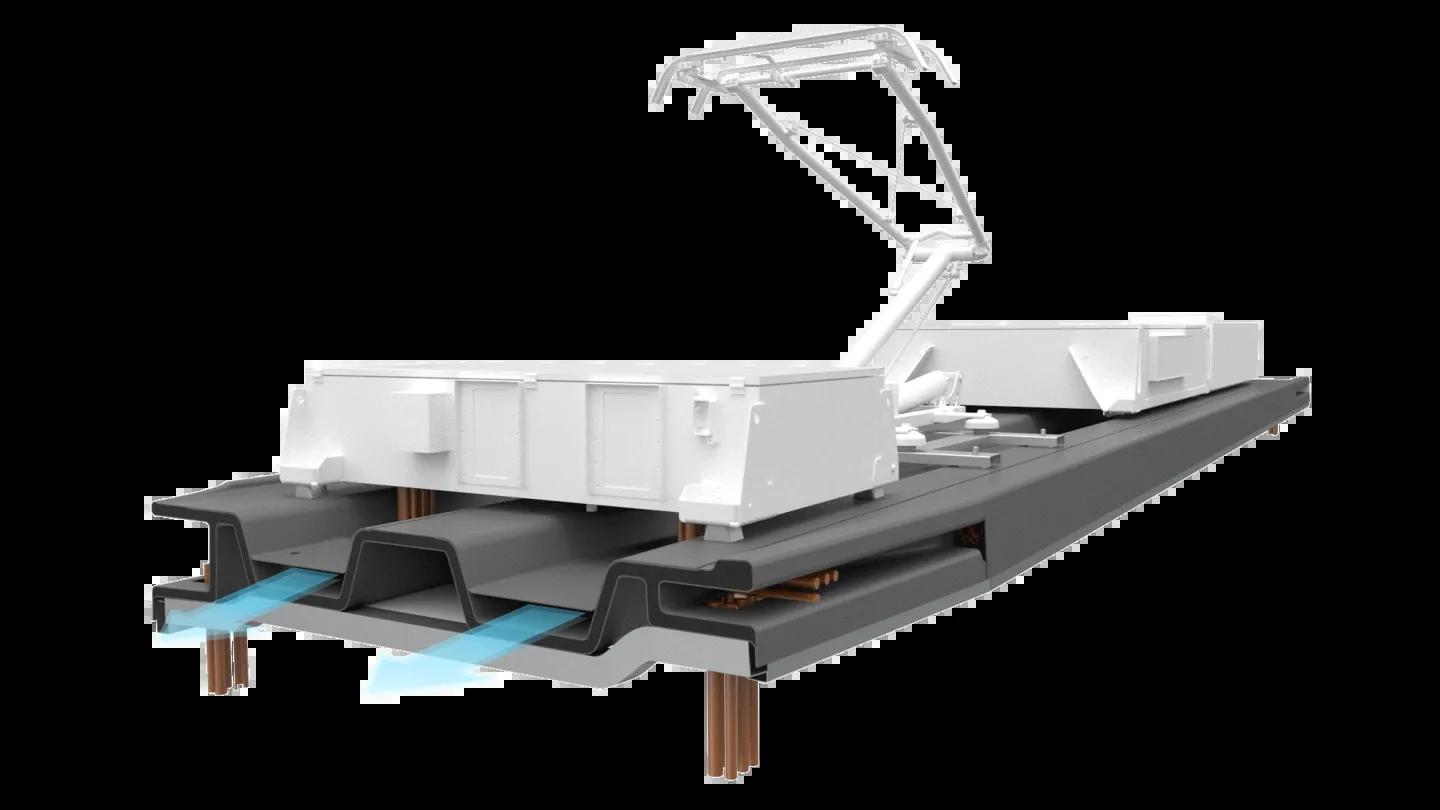
FunPul
Inline functionalization of pultrusion profiles
In the project, the partners are developing a mechanically functionalized lightweight profile for rail vehicle construction under the leadership of Hörmann Vehicle Engineering GmbH (HVE). The hybrid pultrusion profiles are intended to replace extruded aluminum profiles in the body of a rail vehicle while maintaining cost-efficiency and significantly increasing the degree of lightweight construction.
In parallel, a sensor-based functionalized lightweight element for rotor blades in wind turbines (WT) is being developed in cooperation with FiberCheck GmbH (FC). Here, embroidered strain sensors, which are used for monitoring, are integrated into the pultruded functional components. The hybrid profiles for rail vehicle construction are also being enhanced with a sensory function.
RESOLVE
Resource-efficient lightweight solutions based on novel fiber composite semifinished products with bionically optimized fiber orientation
In the RESOLVE research project, the qualification of the technological approaches is now to be advanced in the area of experimental development - and precisely fitting, bionically supported design methods or construction methods are to be developed. The associated significant increase in economic efficiency, resource efficiency and productivity can significantly expand and diversify the fields of application for continuous fiber-reinforced thermoplastic fiber composite materials, thereby bringing intelligent and climate-friendly lightweight construction solutions into widespread industrial use. Due to the high level of interdisciplinarity of the development content, a cross-industry knowledge and technology transfer is promoted - in line with the funding policy objectives - which makes a valuable contribution to securing Germany as an industrial location. In addition, the project can make a significant contribution to achieving the climate targets, as described in Chapter V.
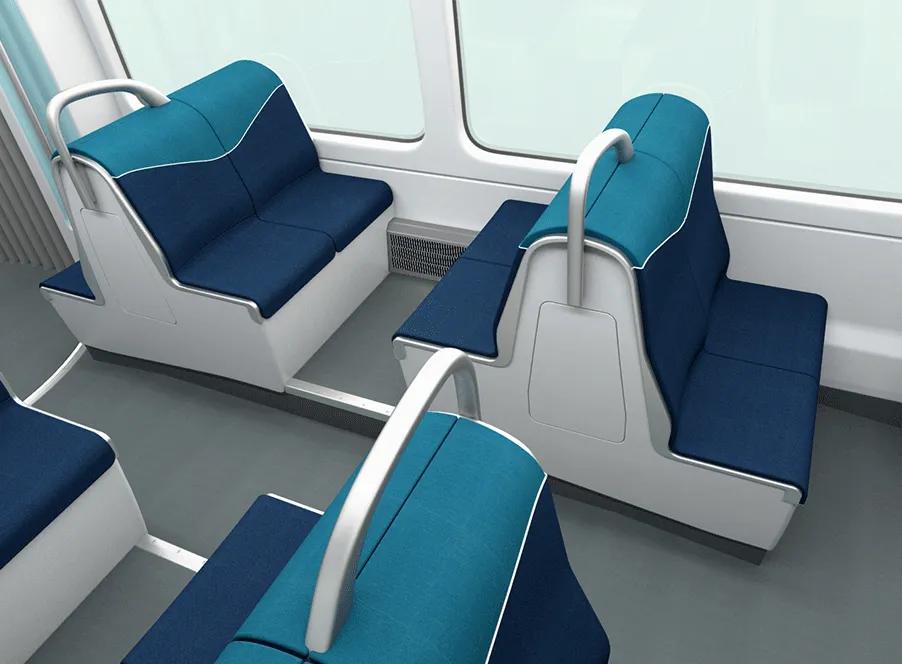
Hybrid Bogie – completed research project
Bogie with a frame of carbon fiber reinforced plastic (CarbonBOGIE)
Project period: Jan 2019 - Sep 2022 | Project partners: KVB Institute, Fraunhofer IWU, IMA Test Center
With the hybridBOGIE joint project, HÖRMANN Vehicle Engineering intends to research a latest-generation bogie (DG). The aim is to create a bogie with improved parameters in terms of functionality, weight, mileage and noise emissions. This is to be achieved by researching a hybrid mixed design with vibration damping materials and the active integration of suspension elements into the functional structure of the bogie frame (DGR).
The aim of the project is the development of a manufacturing process for the production of a hybrid fiber bogie frame including the demonstrator and sample construction. The design and integration of a sensor network into the bogie frame for permanent component monitoring is also part of the subproject. A concept to protect the impact-sensitive frame structure from stone chipping is also being researched.
The project was funded by: EFRE and SAB
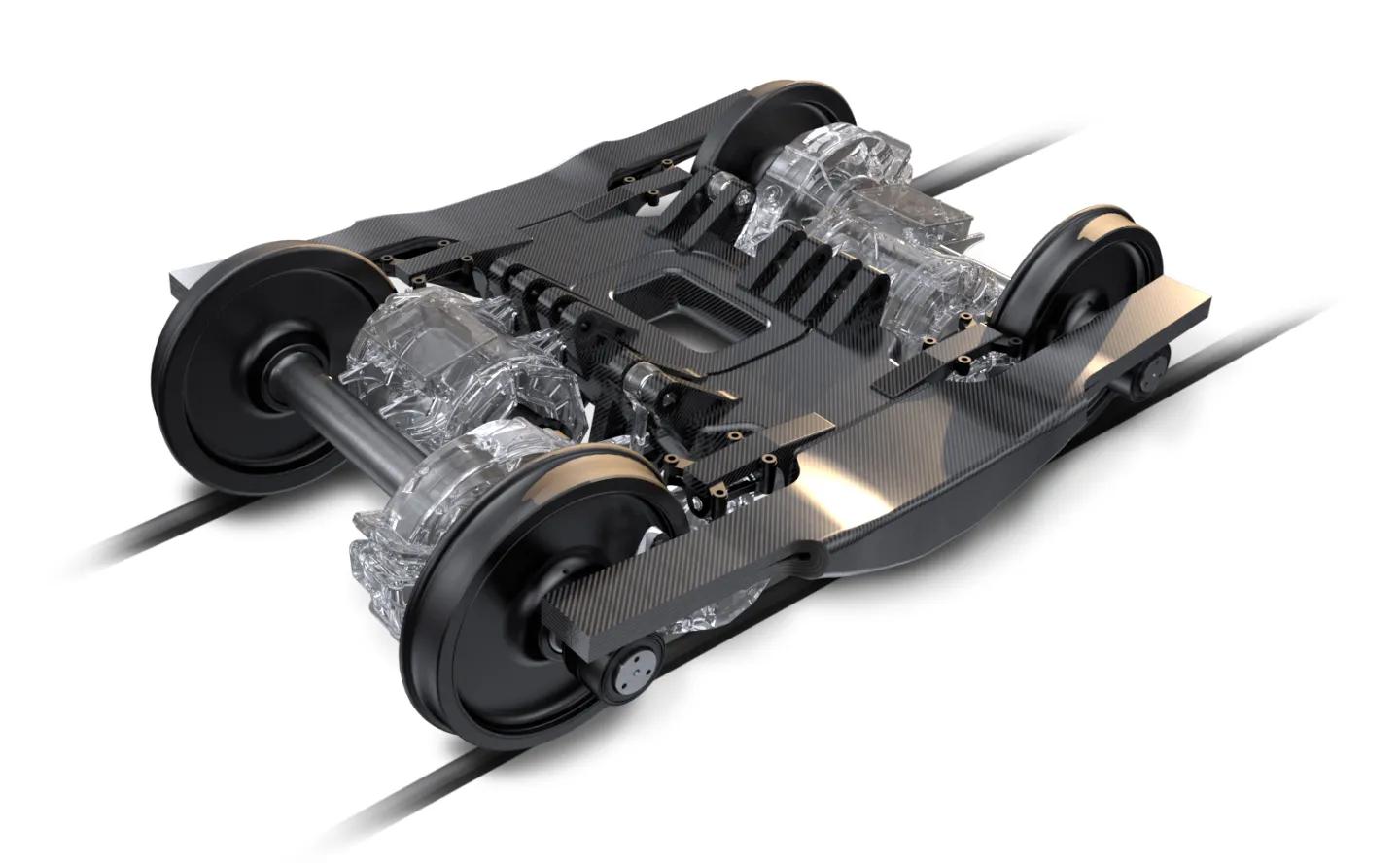
Thermopre+ – completed research project
Manufacturing technology for the reliable processing of load-compatible effiLOAD preforms for flame-resistant interior applications
Project period: Oct 2018 - Oct 2022 | Project partners: Fraunhofer IWU, Hegewald & Peschke, Renolit SE, Norafin, Cetex
In a joint project with regional industrial partners and research institutes, lightweight fiber-plastic composites (FRP) with their special mechanical properties (high-performance polymers) are to be processed into semi-finished products, so-called prepregs, and used in high-performance structural components in automotive and rail vehicle construction. On the basis of novel load-dedicated fibre composite structures (effiload semi-finished products), HÖRMANN Vehicle Engineering, as the composite coordinator is designing a one-piece innovative streetcar seat. This seat is to be 25 percent lighter than comparable seat components and should considerably reduce the assembly work. Due to their short cycle times in component production, such thermoplastic fibre composite components have great potential for series applications.
The project was funded by: Federal Ministry of Education and Research and PtJ
Innovative lightweight chassis – completed research project
HÖRMANN Vehicle Engineering supported HÖRMANN Automotive GmbH in the development of a new integral chassis concept for light commercial vehicles. In terms of production technology, the concept is based on the results of the successfully completed Collaborative Research Centre 666 "Integral Sheet Metal Structures of Higher Branch Order - Development, Production, Evaluation" of the Technical University of Darmstadt. It applies the technologies developed there to vehicle construction for future urban delivery traffic. It uses the branched sheet metal structures to realize new protection mechanisms for energy storage systems of vehicles with alternative drives.
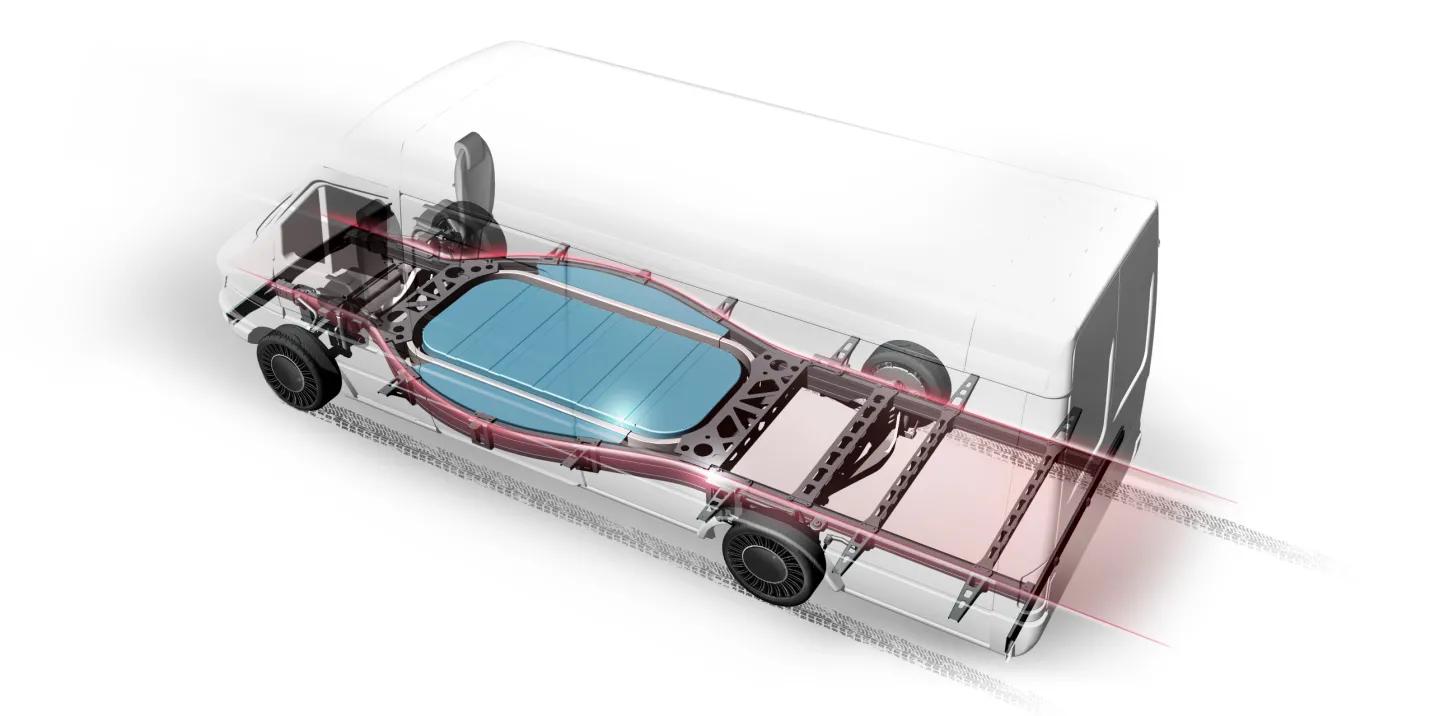